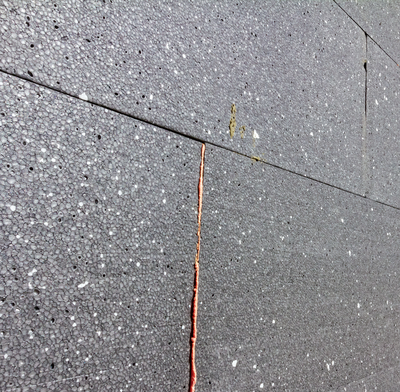
Effective Insulation for Years!
Modern building insulation solutions provide both thermal and humidity comfort as well as an aesthetically pleasing effect. However, an important yet often overlooked aspect is the durability of the achieved results.
Insulation: A Way to Save Energy and Money
High heating bills are often caused by heat escaping from buildings. This happens because the structure lacks proper sealing and insulation. By insulating exterior walls, ground floors, foundations, and roofs, heating bills can be reduced by up to 50%. Styrofoam is one of the most efficient insulation materials, offering a very low thermal conductivity coefficient at a relatively low cost compared to alternative methods.
Why Styrofoam?
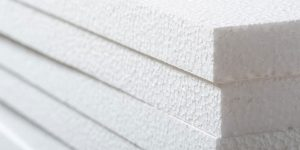
Insulation is subjected to various factors from the moment it is applied. These influences can be categorized as:
- Physical: temperature changes, moisture, UV radiation.
- Chemical: air pollution, acid rain.
- Mechanical: direct damage or stress-related wear.
- Biological: microorganisms, mold, and fungi.
Styrofoam is highly effective for insulation due to its resistance to biodegradation, mold, and fungi. Additionally, its expanded polystyrene structure resists water absorption, with only minimal water penetration occurring in spaces between granules. However, like many other building materials, Styrofoam requires adequate protection from external factors to maintain its technical properties.
Grey Styrofoam Insulation
Graphite-infused Styrofoam has become increasingly popular in recent years among investors and contractors due to its numerous advantages.
Thanks to the addition of graphite granules, grey Styrofoam has improved thermal insulation properties. Its reduced thermal conductivity allows for excellent insulation performance even with thinner panels. Grey Styrofoam meets regulatory standards and is ideal for energy-efficient and passive houses.
However, exposure to UV rays can cause grey panels to expand under heat or melt slightly. The enhanced thermal properties, combined with the dark color, make these panels heat up faster. To mitigate this, installation should be performed using scaffolding covered with protective nets—a practice recommended for all insulation work.
White Styrofoam Insulation
With white Styrofoam, prolonged exposure to direct sunlight can cause yellowing and, over time, surface erosion. Before continuing with further work, any affected surfaces should be sanded down.
The durability of expanded polystyrene (EPS) depends on its structure and application. Proper installation requires the addition of protective layers to shield the material from external factors.
The outermost layer of the insulation system, a thin plaster coating, is especially vulnerable to damage due to its direct exposure to the environment. Regular inspections and the use of biocide-containing plasters and coatings are advisable.
Advantages of Styrofoam Insulation
Styrofoam insulation offers numerous benefits:
- Mechanical Resistance: Ensures stability and retains its shape throughout its use.
- Lightweight: The low weight of EPS panels does not significantly stress the building’s structural framework.
- Ease of Handling: Styrofoam is easy to cut and shape, making it user-friendly during application.
- Compatibility: It works well with most materials used in insulation processes. However, it should avoid contact with organic solvents, bitumen, asphalt, tar, gasoline, and diesel.
By using high-quality materials and ensuring proper application, Styrofoam insulation will retain its insulating and durability properties over time. Maintenance will typically involve only minor repairs and general upkeep, resulting in long-lasting efficiency and aesthetic appeal.